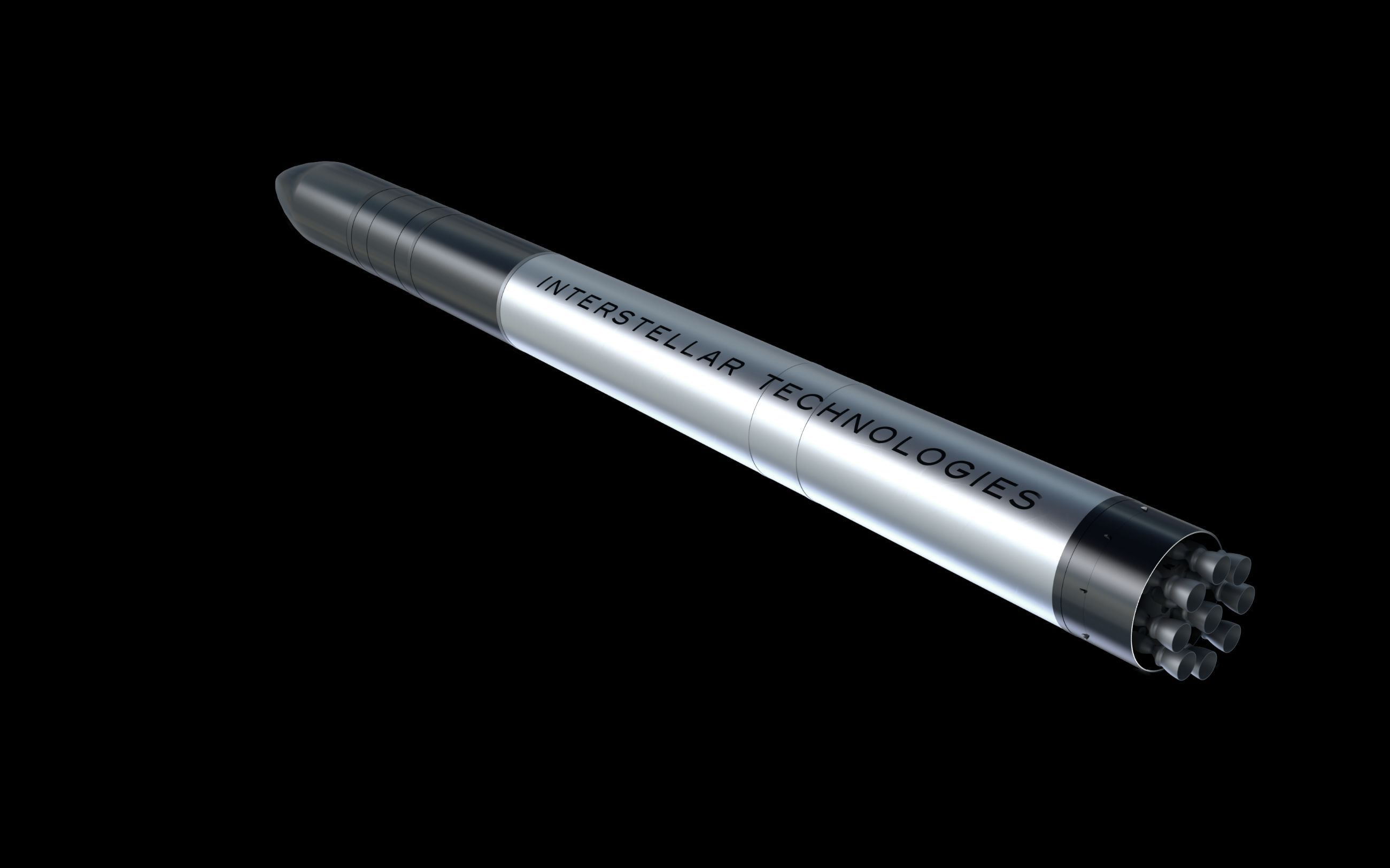
ORBITAL CLASS LAUNCH VEHICLE
Ensuring your small satellite reaches the orbit you desire with flexible space transportation services, including dedicated launches and ridesharing, all on your schedule.
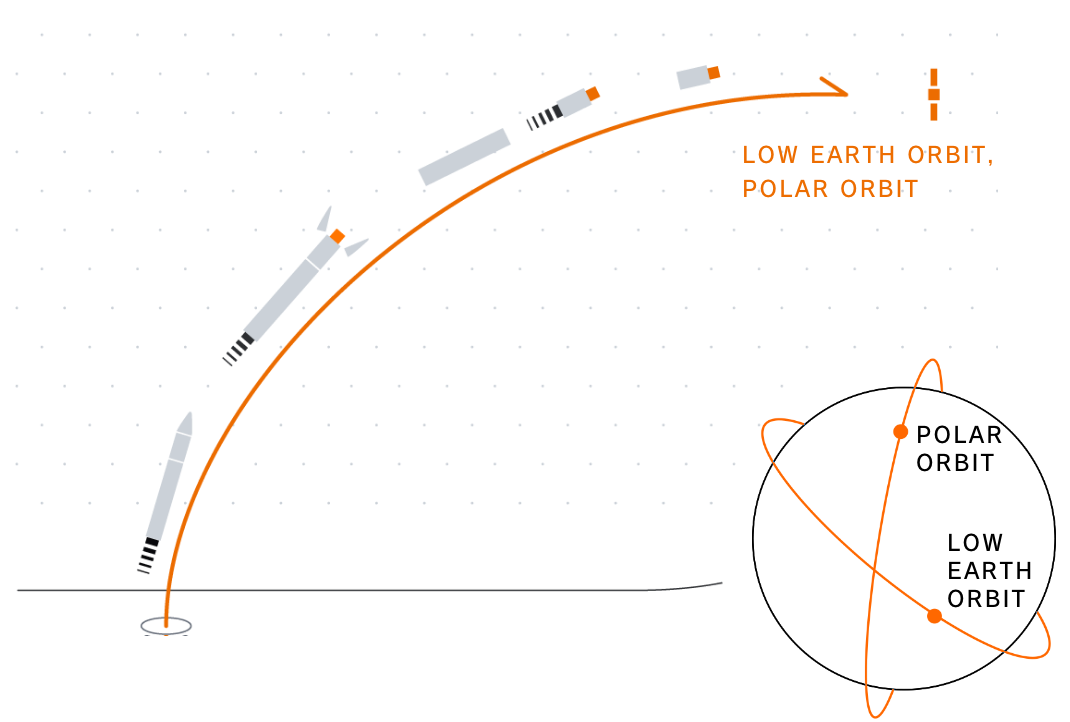
ADVANTAGES
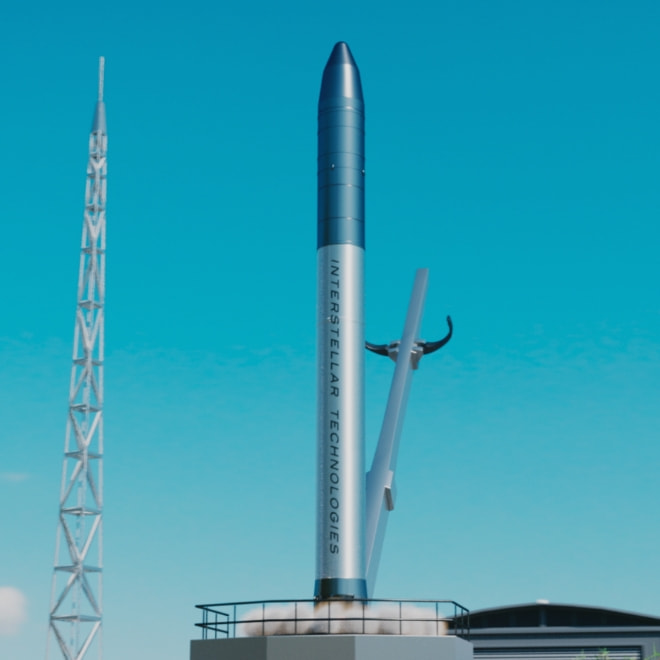
Your Destination,
Your Timeline
Providing on-demand transportation services to reach desired orbits and altitudes, offering a dedicated solution that addresses the limitations of shared transportation for large satellites. Seamlessly integrate in-house design, manufacturing, testing, and launch operations to significantly reduce the time from contract signing to launch.
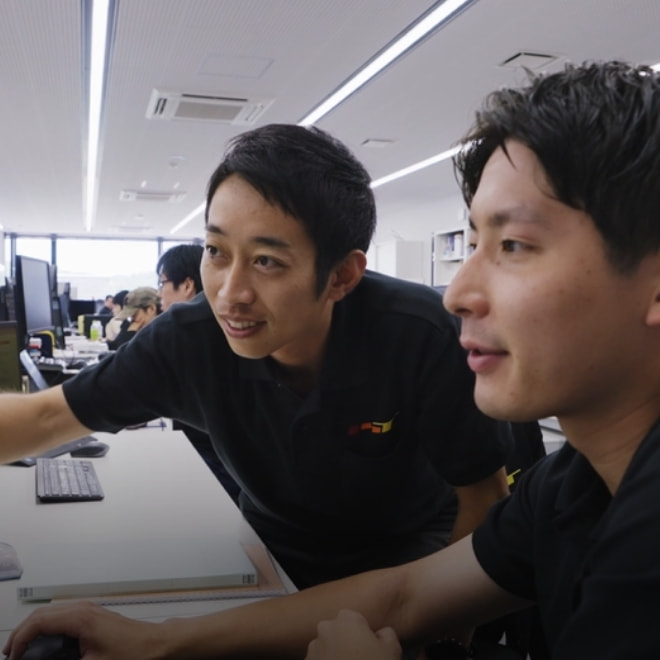
Dedicated
Launch Service
In-house design and manufacturing capabilities grant flexibility to meet your needs. Customizing the system to match your requirements and handling sudden changes ensures high customer satisfaction.
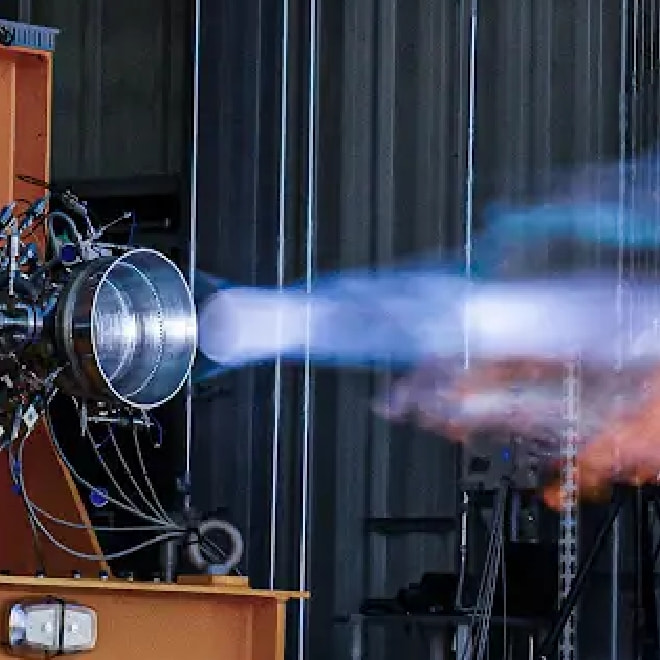
Globally Competitive
Launch Costs
Offering one of the most competitive price points in the small satellite launch market. We strive to reduce prices through the in-house development of core technologies and the active utilization of cutting-edge technologies such as consumer-grade components and 3D printing.
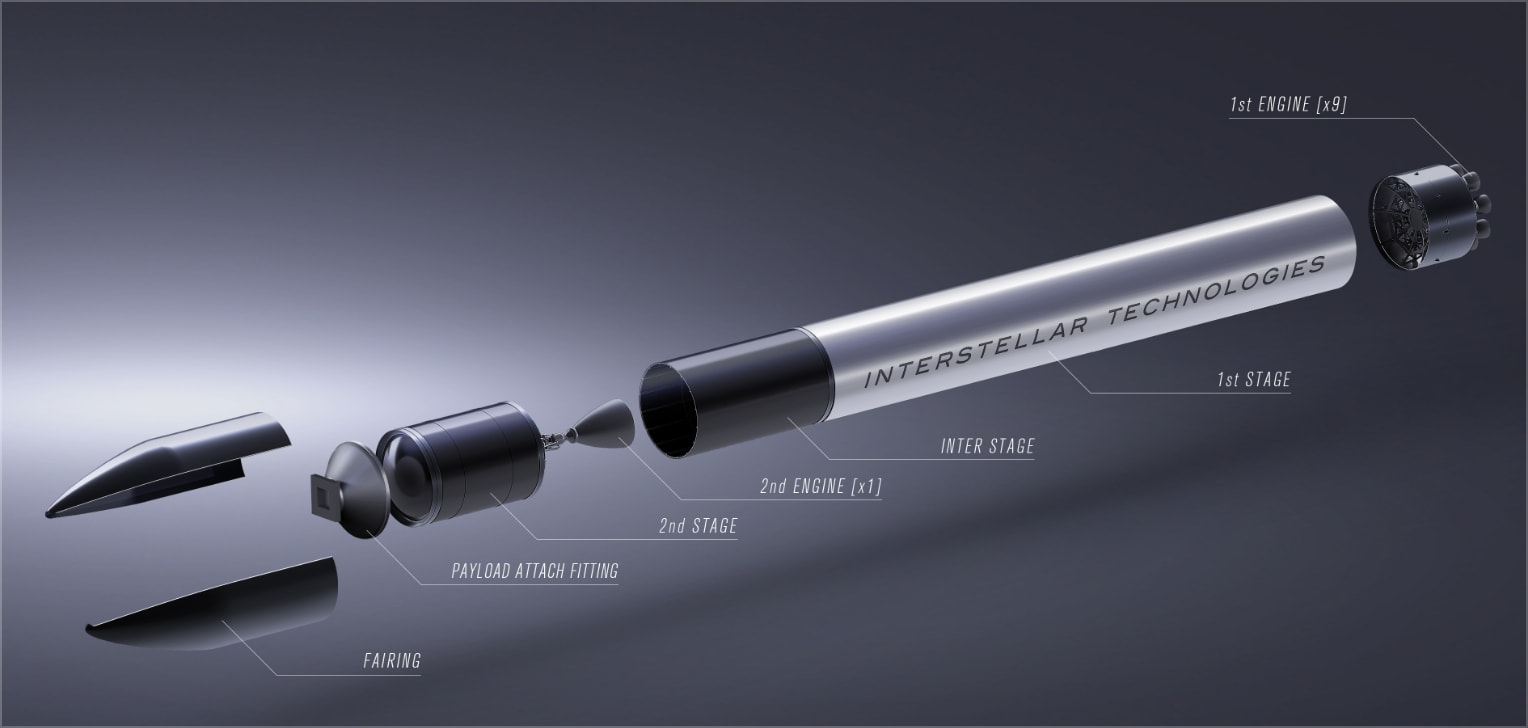
- Two-Stage Rocket: A two-stage rocket designed for satellite launches into orbit
- Versatile Orbits: Versatile orbit options, ranging from low inclinations to polar
SPECS
- ORBIT&ALTITUDE
- LEO
- MAX PAYLOAD WEIGHT
- LEO 1,000kg
- LENGTH
- 32m
- DIAMETER
- 2.3m
- TOTAL WEIGHT
- 71 tons
- PROPELLANT
- Fuel: Liquid Methane
Oxidizer: Liquid Oxygen
COMPONENTS
- 1.FAIRING
Made of CFRP (Carbon Fiber Reinforced Plastic) to protect the payload during transportation.
- 2.PAYLOAD SECTION
For carrying satellites into space.
- 3.SECOND STAGE TANKS
For liquid methane and liquid oxygen, constructed from aluminum alloy.
- 4.SECOND STAGE ENGINE
Engine for reaching orbit, with a high expansion ratio nozzle.to reach orbit.
- 5.FIRST STAGE TANKS
Aluminum alloy tanks housing liquid methane and liquid oxygen.
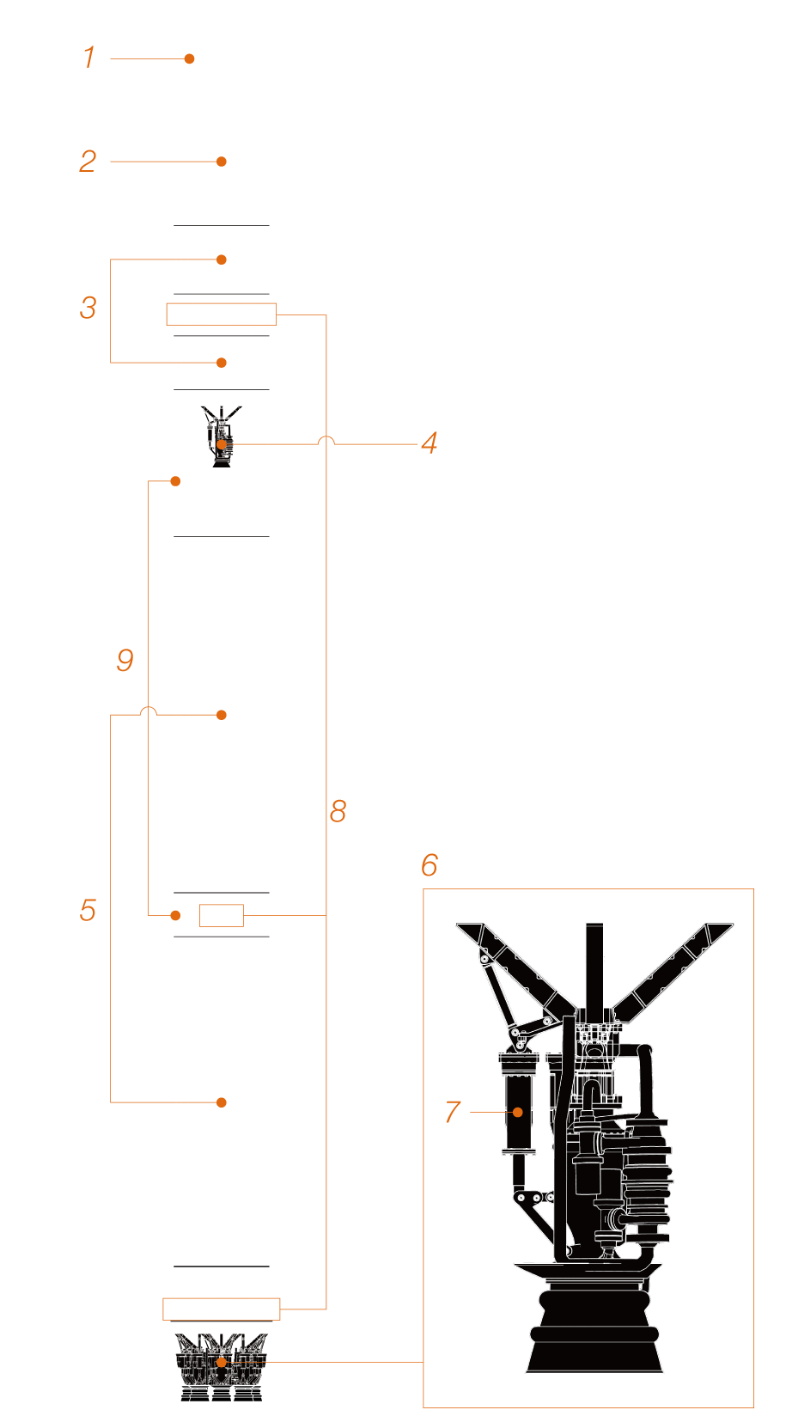
- 6.FIRST STAGE ENGINES
Designed to propel the rocket into space, each of the nine engines has a thrust capacity of approx. 130kN (about 13 tons) and is equipped with regenerative cooling and turbopump technology. During flight, these engines are jettisoned along with the first stage tank.
- 7.ATTITUDE CONTROL SYSTEM
Gimbal mechanisms enable the engines to change direction and control the rocket's flight.
- 8.AVIONICS
Equipped with computers, sensors, and communication devices for controlling the rocket.
- 9.FUSELAGE STRUCTURE
Adopts a sandwich structure with an aluminum core material sandwiched between CFRP.
TECHNOLOGIES
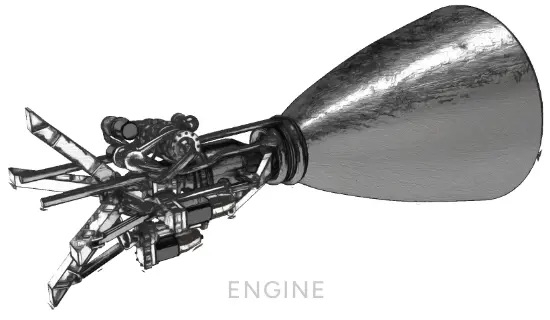
ENGINE
ZERO is a bipropellant rocket that uses liquid bio-methane as fuel and liquid oxygen as an oxidizer. This represents Interstellar's first use of a gas generator cycle, where part of the propellants is burned in a gas generator to drive a high-speed turbopump. This turbopump operates at tens of thousands of rotations per minute, delivering fuel to the combustion chamber under high pressure. The rocket also employs regenerative cooling, utilizing the fuel to effectively cool the combustion chamber walls. The engine for ZERO has been named COSMOS by the development team, inspired by the COSMOS flower, the official flower of Taiki. The engine's pintle injector spray pattern resembles the petals of this flower, making the name a fitting tribute.
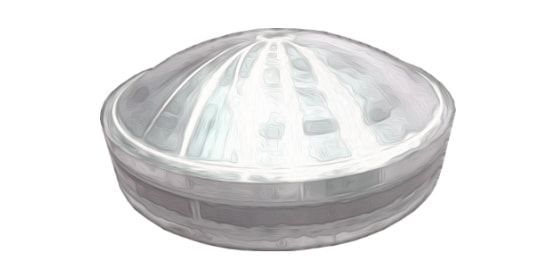
PROPELLANT TANKS
Design, manufacturing, welding, and testing of the tanks are done at Interstellar. High-strength aluminum alloy is used for the tanks that will store the liquid biomethane fuel and liquid oxygen oxidizer. A proof and a burst pressure test were done to ensure its capability to withstand design pressures and to gauge the pressure endurance limits.
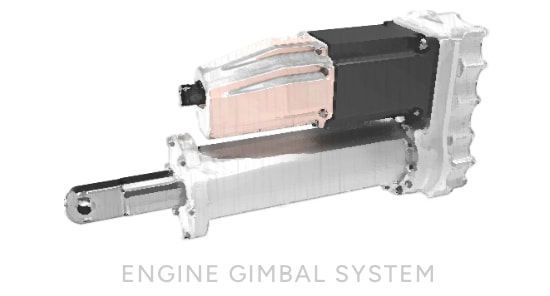
GIMBAL MECHANISM
Gimbal mechanism controls the direction of each engine and consequently the launch vehicle trajectory and orientation. This allows engine adjustments mid-flight, improving safety for the missions. This technology has been demonstrated in our suborbital launch vehicle MOMO.
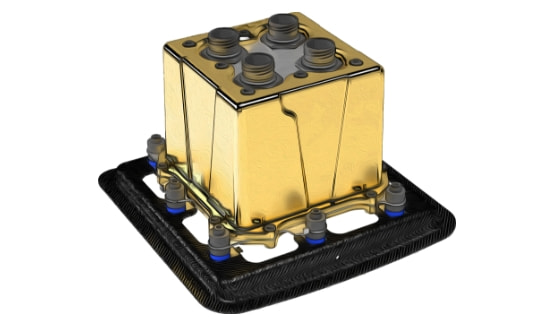
AVIONICS
The avionics system serves a mission critical role in ZERO as it holds the responsibility of monitoring and controlling the safety of the vehicle. The architecture, mechanical hardware, electronic hardware, FPGA, and software development of the avionics system of ZERO are all done in-house at Interstellar.